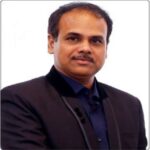
Prof. Pijush Ghosh
Dept of Applied Mechanics and Biomedical Engineering
Prof. Pijush Ghosh
Research Areas
Polymer Membranes, Polymer-polymer interface characterization, Biopolymers: Molecular modeling and experiments, Nano mechanics, Molecular dynamic simulations.
People
Phd Scholars
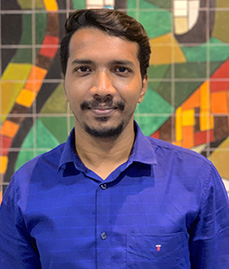
Vijith S– Ph.D. scholar
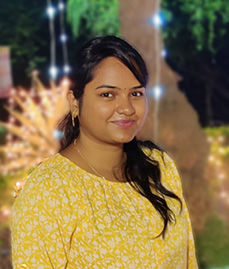
Smruti – Ph.D. scholar
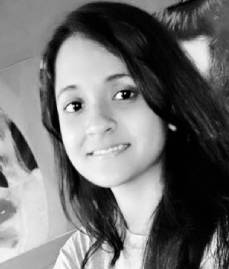
Sanghamitra Debta – Ph.D. scholar
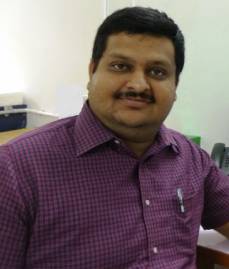
Ashwin K N– Ph.D. scholar
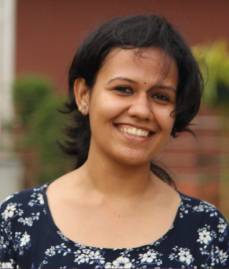
Nidhi Murali – Ph.D. scholar
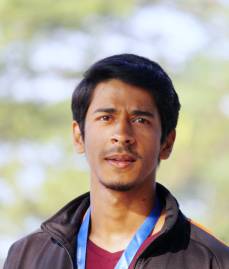
Amit Kumar – Ph.D. scholar
MS Students
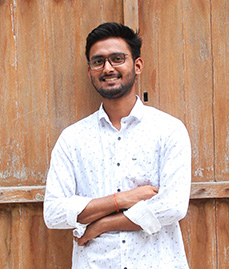
Pawan Kumar– Ph.D. scholar
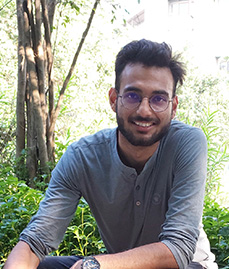
Chaitanya Joshi – Ph.D. scholar
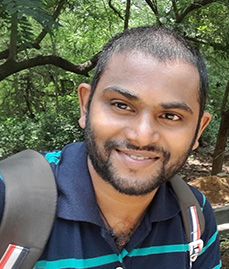
Arunkrishnan - Senior Project Associate
Research
4D PRINTING OF BIOPOLYMERS
1.4D printing defined as “3D printing + time” with the fourth dimension to be time. 4D printing refers to single-material or multi-material printing of a device or object that can be transformed from a 1D strand into pre-programmed 3D shape, from a 2D surface into preprogramed 3D shape and is capable of morphing between different dimensions.
2. This advanced technology enables us to fabricate dynamic structures which can change their shapes, functions, or properties along with the time when appropriate external stimuli (e.g., water, pH, temperature) are applied.
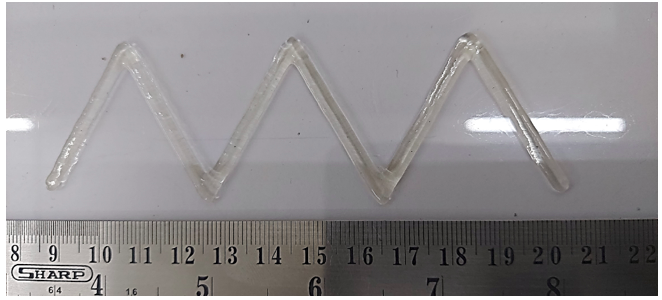
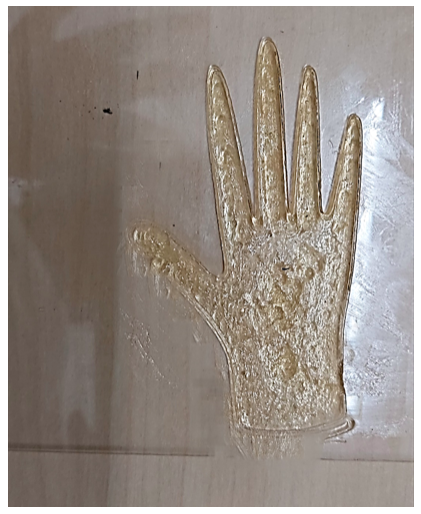
Figure 1: Exploring the Time Dimension in 4D Printing Technology
3D Printer with FDM / DIW Heads
3D Printer with FDM / DIW Heads
We work with stimuli responsive smart biopolymers. We perform different experimental characterization and develop 2D or 3D continuum scale models to predict the behaviors and the mechanisms involved.
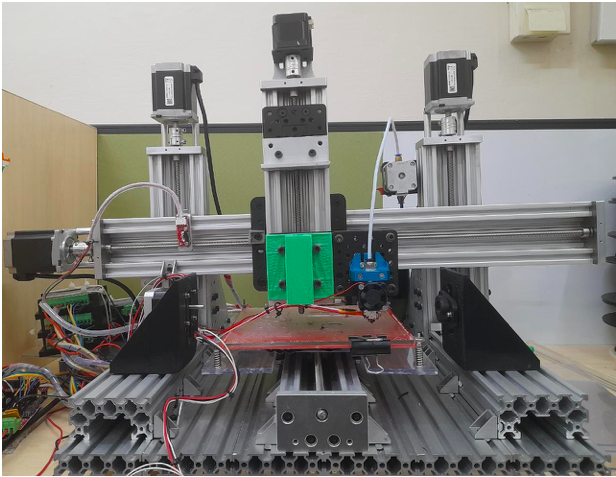
Figure 2: 3D Printer with FDM / DIW Heads
Solvent Triggered Actuation (reversible & irreversible)
Stimuli responsive biopolymers with advanced functionalities have found a wide range of futuristic applications as soft actuators morphing medical devices artificial muscles, and soft robotics, sensors, etc. We work with biopolymers (chitosan, PVA etc) which responds to solvent (water, the simplest one) as external trigger. The films actuate or folds and unfolds when exposed to solvent.
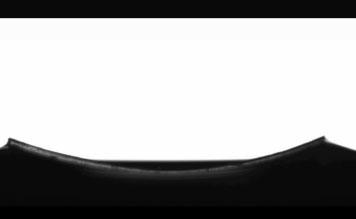
Figure 1: Exploring the Time Dimension in 4D Printing Technology
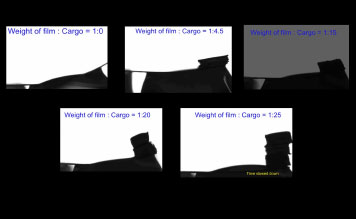
Figure 3: Experiment indicating load carrying ability of thin film during actuation or folding
The folding is due to differential swelling across the thickness of the film caused due to concentration gradient of solvent. During folding, the polymer chains at the bottom layer experience tension, whereas the top layer chains are in compression. With the passage of time, water diffuses further through the layers of the film, reducing the concentration gradient, thus relaxing the polymer chains to go back to their equilibrium state.
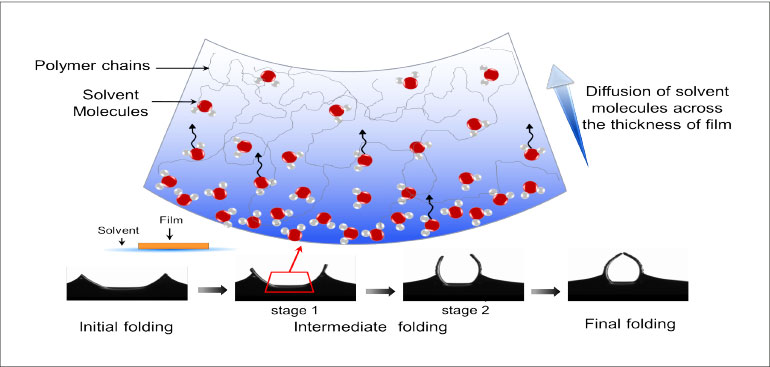
Schematic showing the concentration gradient of solvent molecules developed during folding
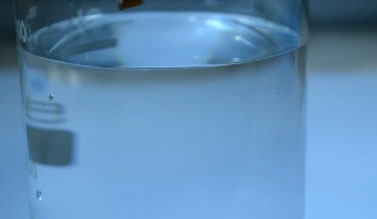
Possible application in gripping of an object
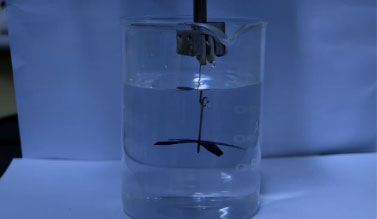
Possible application in wrapping of an object
Interestingly, this folding and unfolding behaviour can be controlled by playing with the properties of the polymer matrix and the solvent. For example, in one of our works, we have added some organic solvent to the water (used as trigger) and could achieve irreversible or permanent folding. This permanent folding behaviour can be used for gripping and lifting some materials.
Dual Triggered Actuation
It is not always possible or even convenient to have water in bulk around to trigger this folding. In one of our works, we have applied pNIPAM layer as a source of water or solvent supply when the temperature goes beyond the LCST of it (which is around 35oC). Figure 1 illustrates the response of chitosan/pNipam bilayer to temperature. As the lower critical solution temperature of synthesized pNipam particles is about 32.5 °C, the actuation of the film begins around 32.5 °C – 35 °C. As exemplified in Figure 1A, upon increasing the temperature to 35 °C, water released by pNipam goes to the chitosan and triggers the actuator to undergo out of the plane folding and unfolding. Figure 1B presents the folded state of the actuator, where the pNipam chains become dehydrated and collapsed due to the increase of temperature above the LCST of the microgels. Figure 1C and Figure 1D represent the unfolded state of chitosan/pNipam bilayer
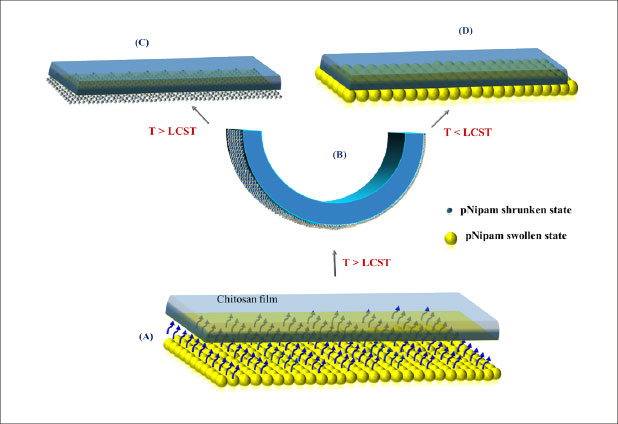
Schematic showing how p Nipam layer can be applied as source of solvent necessary to trigger actuation
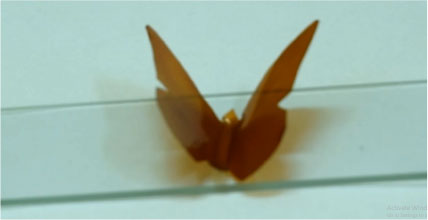
Flipping of the butterfly at 35 degrees centigrade
Continuum Scale Model
As understandable from the above discussion, that diffusion of solvent results in concentration gradient which leads to displacement field, showing up in the form of folding. During this phenomenon, the diffusion affects the mechanical properties of the polymer matrix, which in turn affects the diffusion. Thus it is a coupled diffusion deformation mechanism. we develop a model based on the coupled diffusion-deformation mechanism which can predict the large deformation caused during this reversible folding behavior of a polymeric thin film. The formulation incorporates a concentration dependent Young’s modulus variation. This continuum scale model provides us a detailed insight in to the concentration gradient and strain field developed during the process of folding and unfolding.
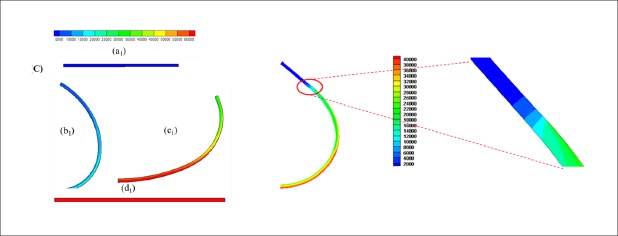
Diffusion Couple Deformation FE Modeling of Folding: Indicating curvature and concentration gradient
MECHANICS OF POLYMER THIN FILMS & NANOCOMPOSITES
We study the mechanical responses of polymer thin films, their interfaces, etc. applying combination of experimental techniques and FEM and/or Molecular Dynamics Simulations depending on the problem need. Both experimentally and through continuum models, we characterize, different polymer nanocomposites we synthesize in our lab.
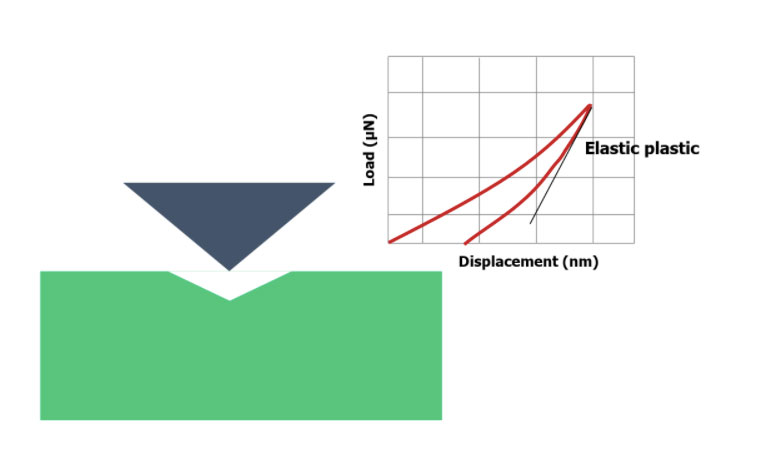
Nanoindentation and Load-Displacement Plot
Thin Film Interface
We find single and multiple layers of polymer thin film (30 to 500 nanometer thick) in different engineering, electronic, optical, and data storage applications. Tissue regeneration, implants, stents, as well as drug delivery are some of the emerging biomedical applications of thin films. In a thin film system, with two or more layers of coating, an interface plays an extremely important role in determining the overall behaviour, performance and characteristics of the system. We, in our group adopt, nanomechanical techniques including nanoindentation, nanoscratch and nano-dynamic mechanical analysis (nanoDMA) to study and characterize these interfaces.

Schematic diagram showing strain distribution on wrinkled surface at different regions
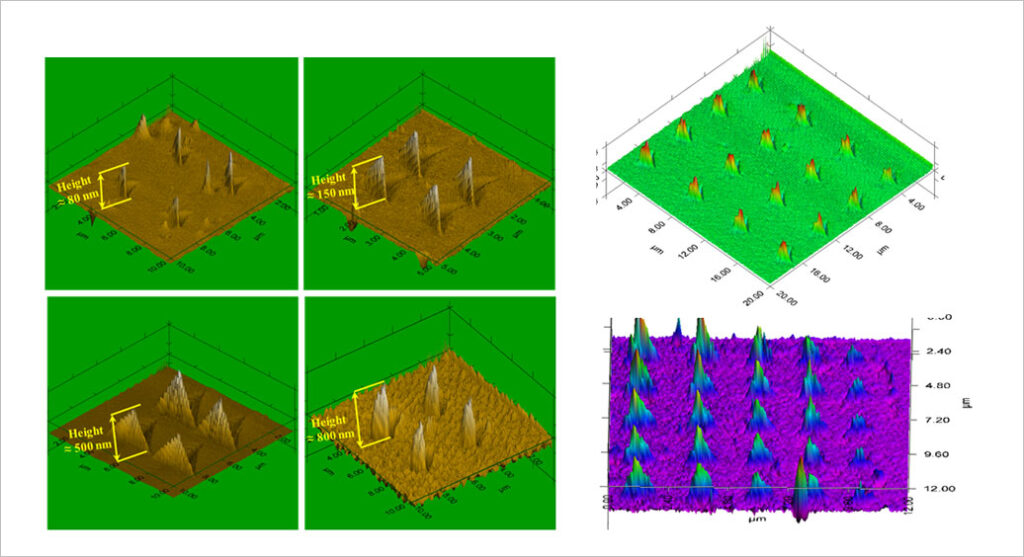
Synthesis of Nanopillar of uniform and varying size taking help of Nanoindentationnt
Confined Thin Films
One of the major difficulties that we encounter while measuring the modulus and hardness of thin film is the ‘substrate effect’. Basically, when you are indenting and going past certain depth, the properties of the substrate start influencing your measured film properties significantly. Then we need to separate out this substrate effect from the measured composite values. This ‘substrate effect’ however, can also be used to our advantage. For example, in one of our works, we have determined the property of an inaccessible substrate, under changing temperature environment, making use of this ‘substrate effect’. We used experimental data and Finite Element Modeling in the same study to determine the necessary properties (including glass transition temperature of the substrate).
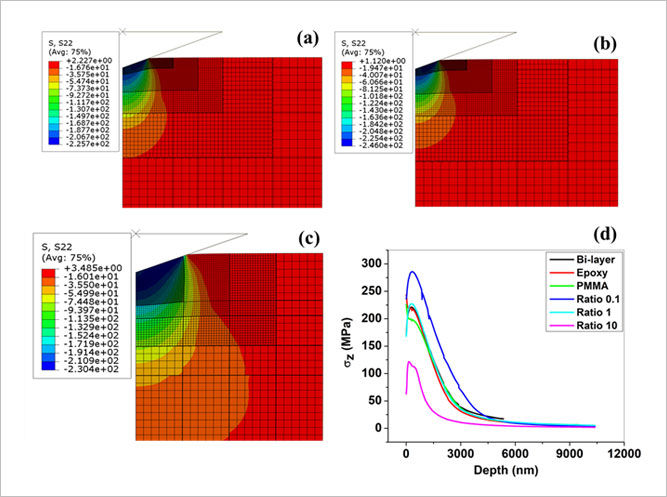
Stress contours beneath the indenter for (a) PMMA, (b) epoxy, (c) bi-later at 300C (d) The variation of sz beneath the indenter obtained from FEA
Projects
4D printing of biopolymer
4D printing defined as “3D printing + time” with the fourth dimension to be time. 4D printing refers to single-material or multi-material printing of a device or object that can be transformed from a 1D strand into pre-programmed 3D shape, from a 2D surface into preprogramed 3D shape and is capable of morphing between different dimensions. This advanced technology enables us to fabricate dynamic structures which can change their shapes, functions, or properties along with the time when appropriate external stimuli (e.g., water, pH, temperature) are applied.
Mechanics of polymer thin films and nano composites
We study the mechanical responses of polymer thin films, their interfaces, etc. applying combination of experimental techniques and FEM and/or Molecular Dynamics Simulations depending on the problem need. Both experimentally and through continuum models, we characterise, different polymer nano-composites we synthesise in our lab.
Outreach activities : https://www.teachtolearn.co.in/
Facilities
FTIR TENSOR II FTIR
FTIR TENSOR II FTIR Spectrophotometer from Bruker Optics
Fourier Transform Infrared Spectroscopy, also known as FTIR Analysis or FTIR Spectroscopy, is an analytical technique used to identify organic, polymeric, and, in some cases, inorganic materials. The FTIR analysis method uses infrared light to scan test samples and observe chemical properties.
NANOINDENTOR- TI
NANOINDENTOR- TI Premier(Bruker Hysitron)
A nanomechanical test instrument which deliver the highest degree of performance, accuracy, reliability, and versatility for quantitative mechanical and tribological characterization at the nanoscale and microscale.
Collaboration
to be added
Publication
- Solvent-Responsive Functionally Graded Hydrogel Thin Films for Programmed Actuation S Debta, PY Kumbhar, P Ghosh, RK Annabattula ACS Applied Engineering Materials 2024
- Role of particle gradation of clay–sand mixtures on the interfacial adhesion performance of polymer coatings N Murali, J Li, A Agarwal, P Berthault, P Ghosh Clay Minerals, 1-10 2024
- Efficient reduction of the scrolling of Descemet membrane endothelial keratoplasty grafts by engineering the medium N Gupta, A Kumar, PK Vaddavalli, NR Mahapatra, A Varshney, P Ghosh Acta Biomaterialia 171, 239-248 2023
- Engineering interfacial strength of polymer coated hydrating cement paste by tuning calcium characteristics P Gujar, N Murali, NK Ilango, M Santhanam, P Ghosh Materials and Structures 56 (3), 65 2023
- Interface Microstructure–Based Mechanical Property Evaluation of CSH A Alex, NK Ilango, P Ghosh Journal of Materials in Civil Engineering 35 (2), 04022431 2023
- Solvent triggered shape morphism of 4D printed hydrogels S Parimita, A Kumar, H Krishnaswamy, P Ghosh Journal of Manufacturing Processes 85, 875-884 20 2023
Social Impact
to be added
Gallery
To be Added